How Component Design Affects Machining Costs
In the realm of manufacturing, the design of a component significantly influences its overall production costs. Precision machining is a critical process where every design decision can impact the ease, speed, and expense of manufacturing. From the material chosen to the complexity of the design, every aspect has a cost implication. This blog post explores key areas where thoughtful design can lead to more cost-effective manufacturing processes. By understanding these factors, designers can optimize their components not only for functionality and aesthetics but also for cost-efficiency in production.
Material Selection
Different materials vary in their machinability. Some materials are harder to cut, require specialized tooling, or have a higher wear rate on tools, all of which can increase costs. For example, nickel-based materials are considerably more challenging to machine than aluminum. The hardness and abrasive properties of nickel alloys can lead to rapid tool wear, requiring that cutting tools be checked constantly to ensure that the required tolerances are being maintained throughout the machining process. This constant monitoring increases both the time and cost associated with manufacturing.
Complex Geometries
Designs that include complex geometries, such as deep pockets, thin walls, or intricate details, often require more sophisticated machining strategies, more setup time, and potentially more specialized machinery, which can drive up costs. For both turning and milling, more complex geometries can necessitate additional setups or the use of more expensive equipment like 5-axis mills or mill-turn machines. These machines typically have higher operating costs due to their advanced capabilities, and this directly impacts pricing.
Tolerances
Tighter tolerances, such as .0005" or less, demand more precise machining processes and can substantially increase the cost. This precision requires more passes, slower speeds, and potentially more advanced and expensive machines. Additionally, Geometric Dimensioning and Tolerancing (GD&T) requirements can significantly affect costs. While basic dimensional tolerances might be manageable, very tight positional tolerances can increase the complexity and cost of manufacturing.
Surface Finish
When a design requires a very low roughness average (Ra) value for surface finish, it often necessitates alternative finishing processes outside of traditional machining, such as grinding, lapping, or polishing. Modern cutting tools can generally achieve a finish of 32 Ra, with some exceptions that can go even lower. However, requirements for a surface finish in the single-digit Ra values will significantly impact pricing due to the additional processes involved.
Accessibility and Tool Paths
If a design does not consider how a tool will access various parts of the component, it may require additional setups or even custom tooling to achieve the desired geometry, adding to the cost. A common example of this is the machining of deep pockets, which can drive the programmer to use large tool extensions. These extensions can compromise tool stability, potentially resulting in poor surface finishes or even broken tools, both of which can increase manufacturing time and costs.
Component Size and Scale
Larger or bulkier designs may limit the number of parts that can be machined in a single setup, reduce the speed at which machines can operate, or require larger, more expensive equipment.
Batch Size
Designs optimized for large batch sizes may not scale down cost-effectively to smaller batches. Conversely, a design that is too customized for small batches may be too costly to scale up.
Integration of Features
Overly complex assemblies with many separate parts could be redesigned to be manufactured as a single piece, or with fewer components, reducing the assembly time and overall cost.
Avoiding Undercuts and Internal Corners
These features often require special tooling or multi-axis machining capabilities, which can increase the machining time and cost.
Standard vs. Custom Hole Sizes
Using hole sizes that do not match standard drill sizes can lead to additional costs. Metric drills typically increase in 0.1 mm increments, and imperial sizes increase by 1/32 inch. Designing a component that requires hole sizes outside these standards may necessitate custom drill bits or more complex machining processes, such as boring, which are more costly.
Inspection and Measurement Capabilities
The design must also consider the ability to measure and inspect the parts accurately during manufacturing. If the inspection methods for verifying critical dimensions are not practical or require highly specialized equipment, it can substantially increase the cost. For example, if a part's design makes it difficult to measure key features easily on the shop floor, it may require stopping production to use more advanced measurement techniques or even sending parts out for external inspection. Both scenarios lead to increased manufacturing time and costs, as operators might struggle to maintain the required quality during regular production runs.
Contact Modelcraft Co. For More Information
Optimizing component design for machining is not just about reducing material costs or simplifying geometries; it's about considering a holistic view of how the component will be manufactured, measured, and finished. As we've explored, choices like material selection, tolerances, surface finishes, and even the machine capability necessary for production play pivotal roles in defining the manufacturing costs. Designers must collaborate closely with machinists and production engineers to ensure that the designs are practical to produce while meeting all quality requirements. Ultimately, smarter design decisions upfront can lead to significant cost savings and enhanced manufacturability, benefiting both manufacturers and end-users alike. Contact Modelcraft Co. today for more information and for precision manufacturing services in CT.
Recent Articles
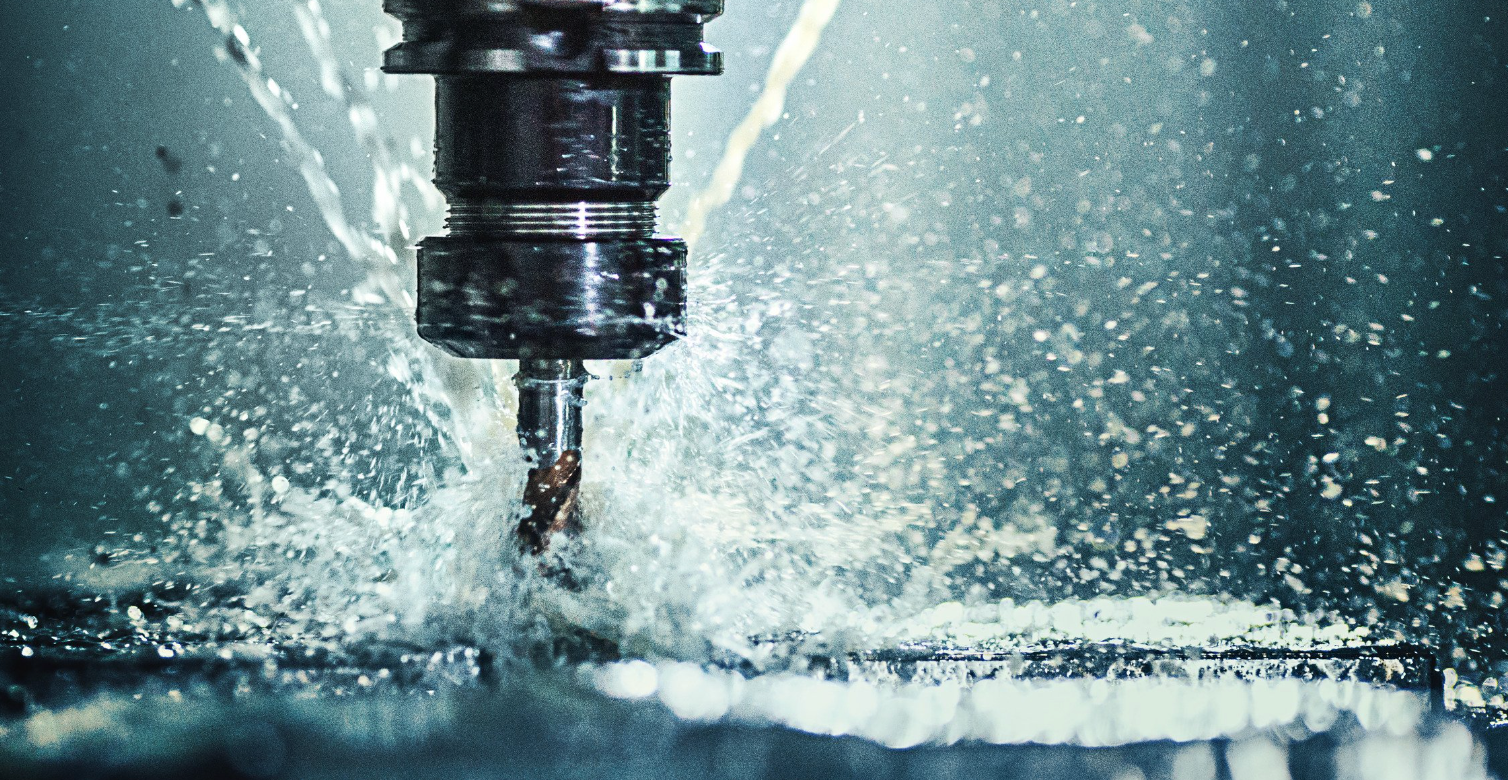
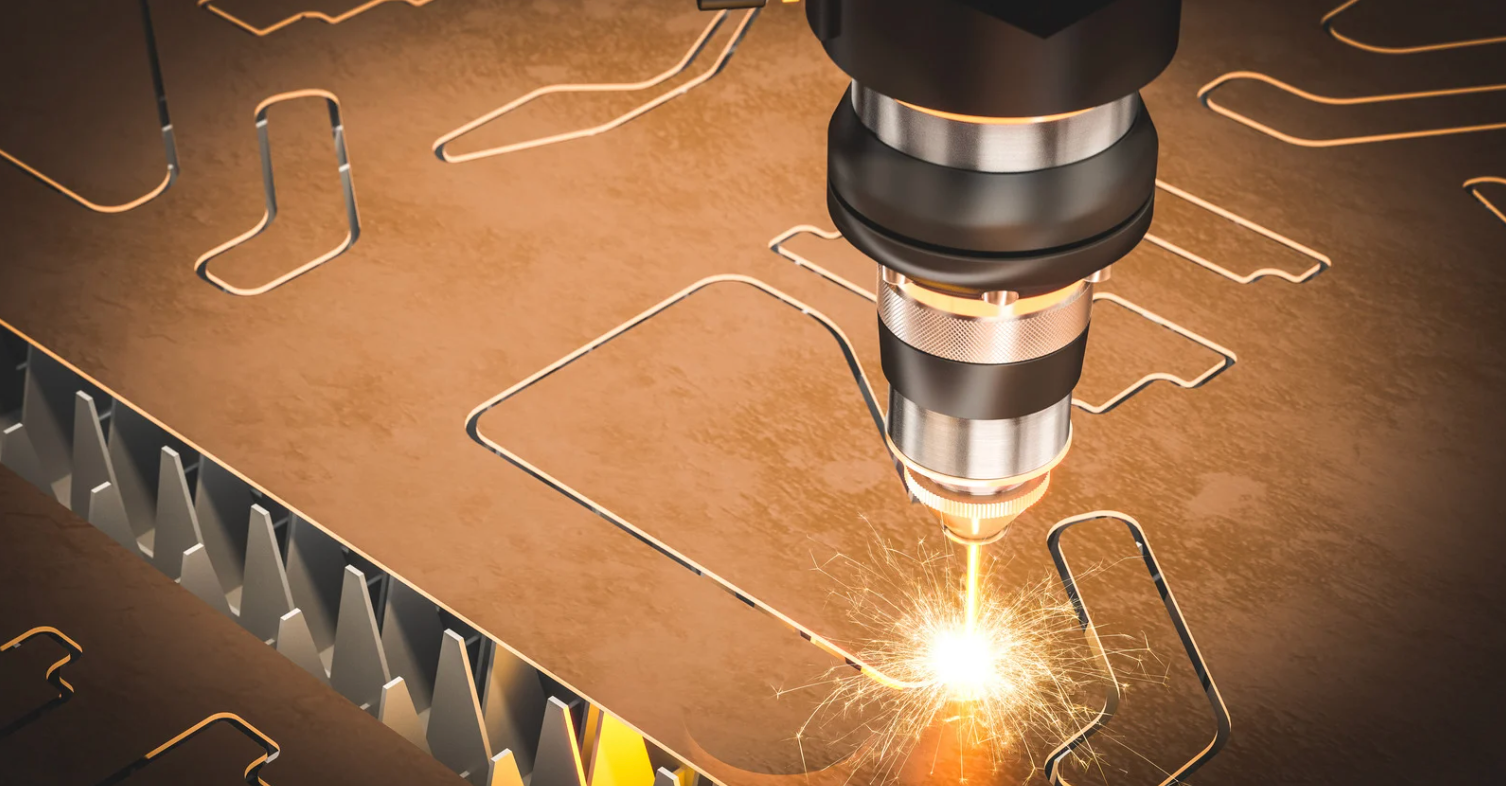

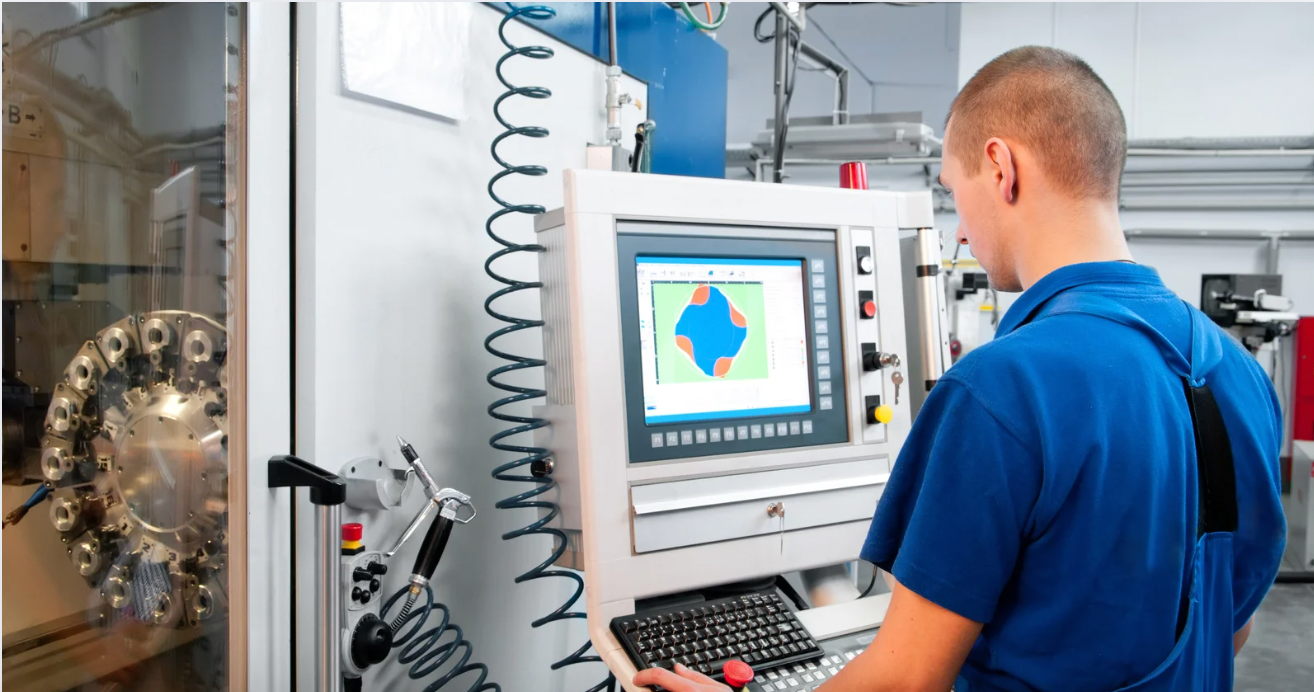
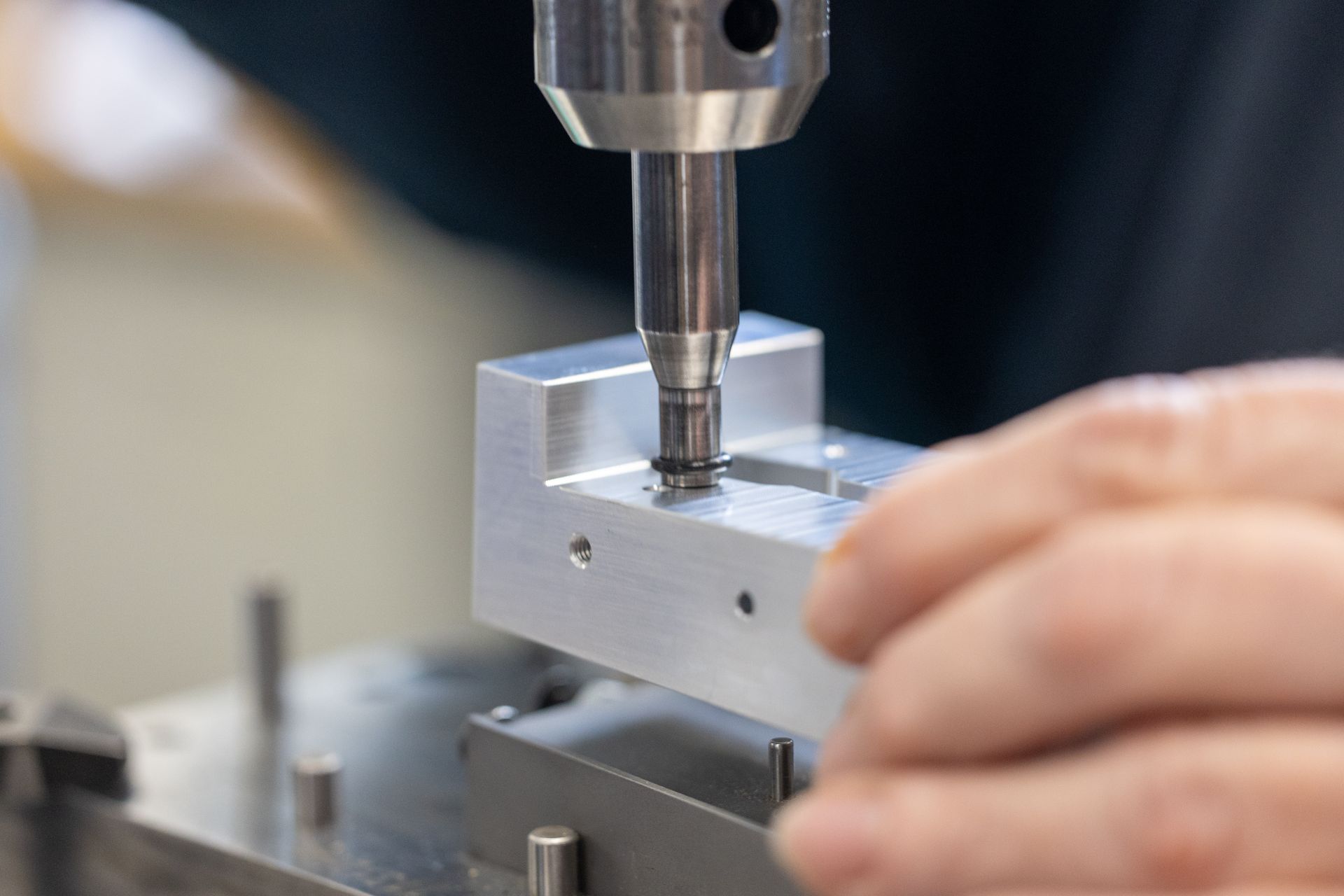
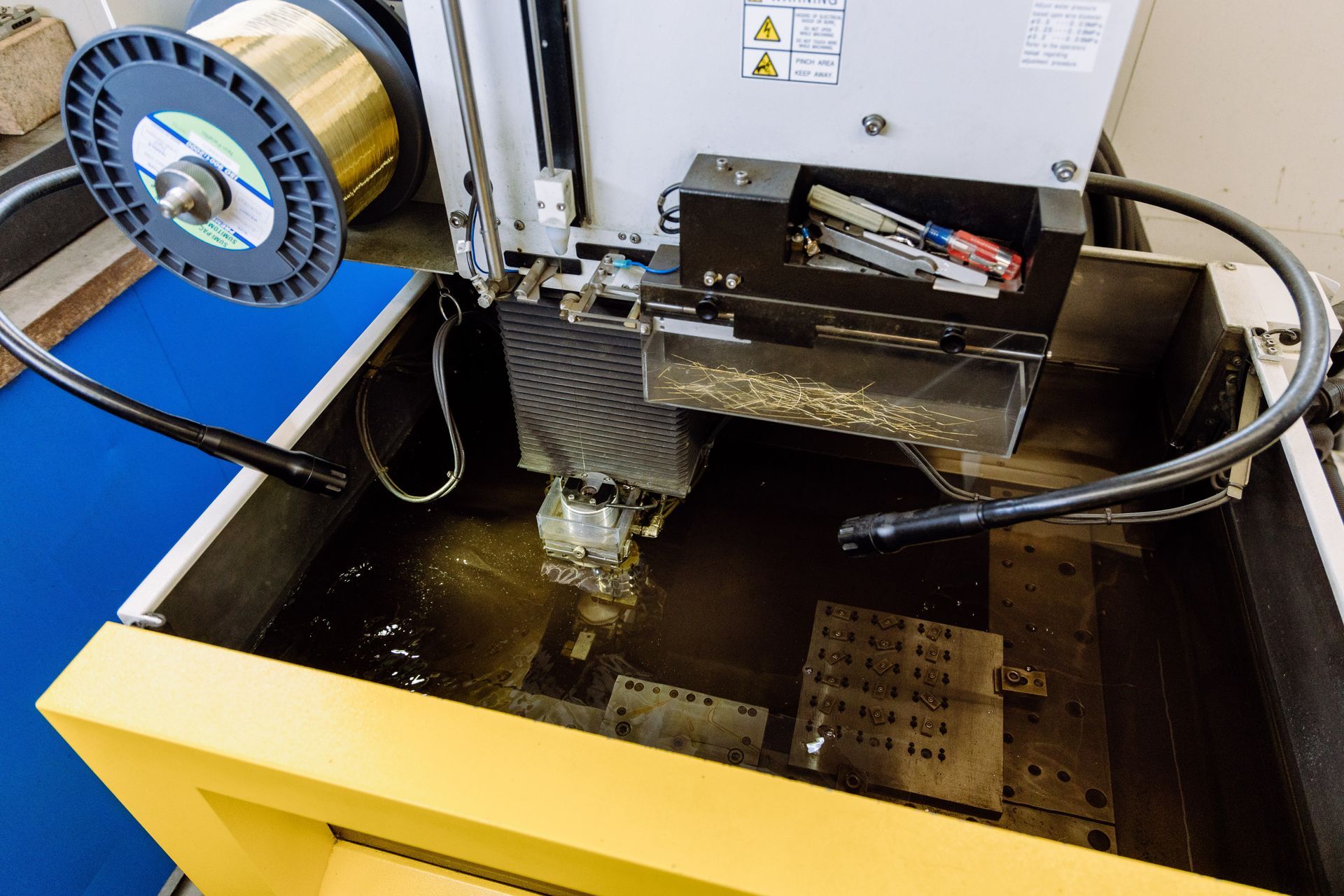
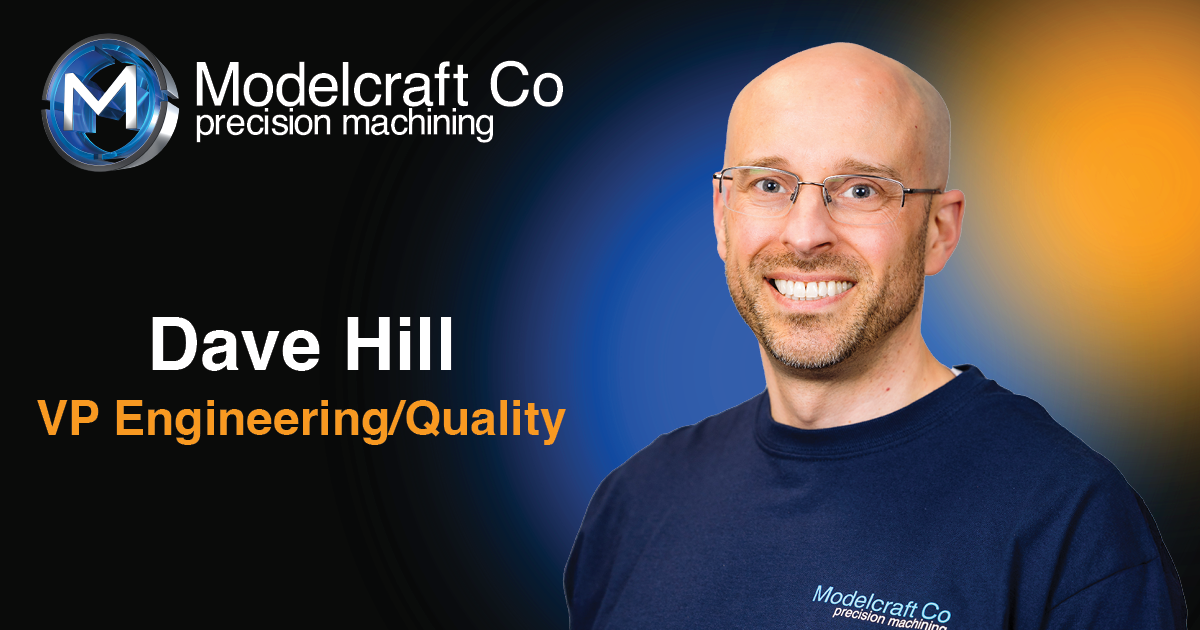
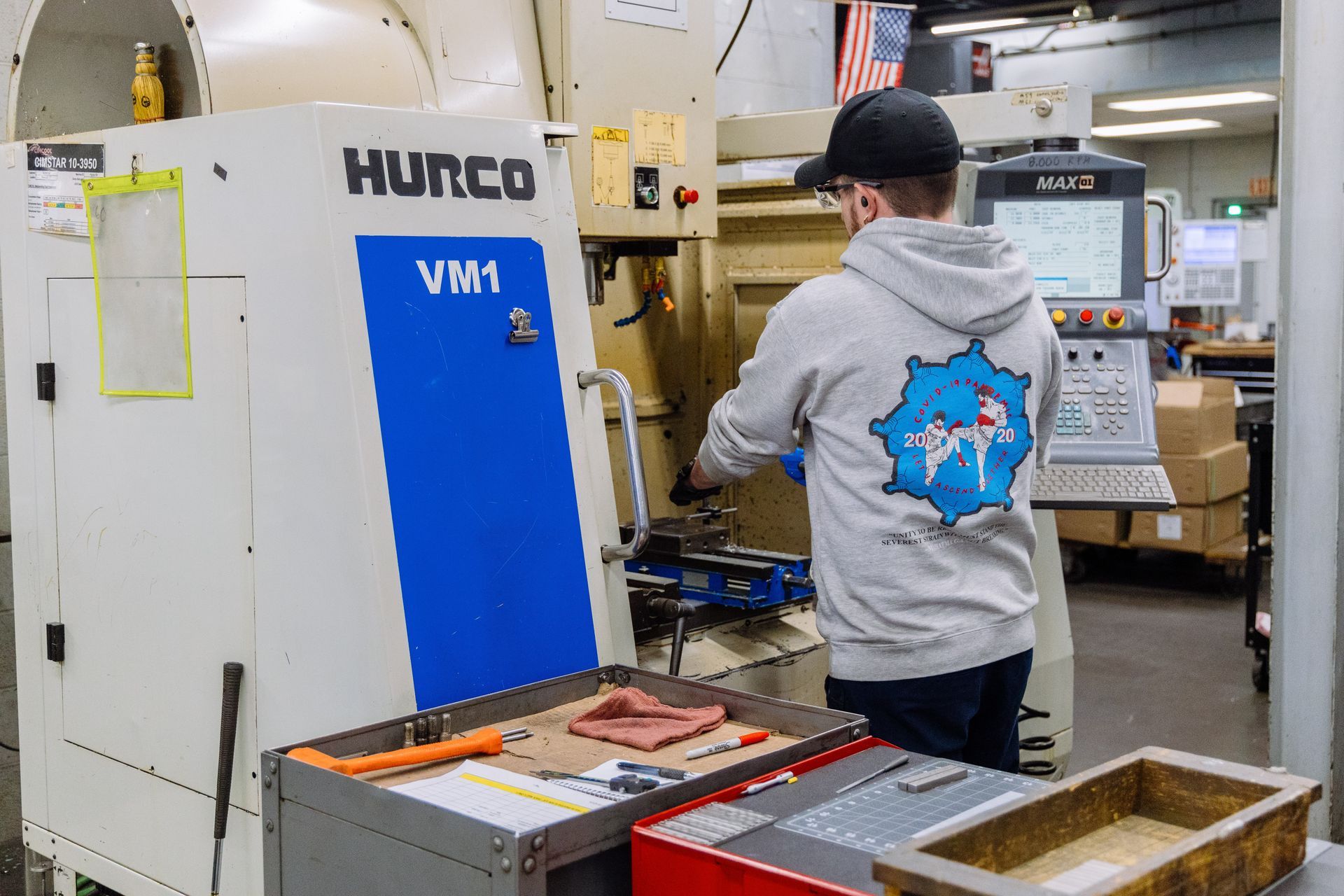
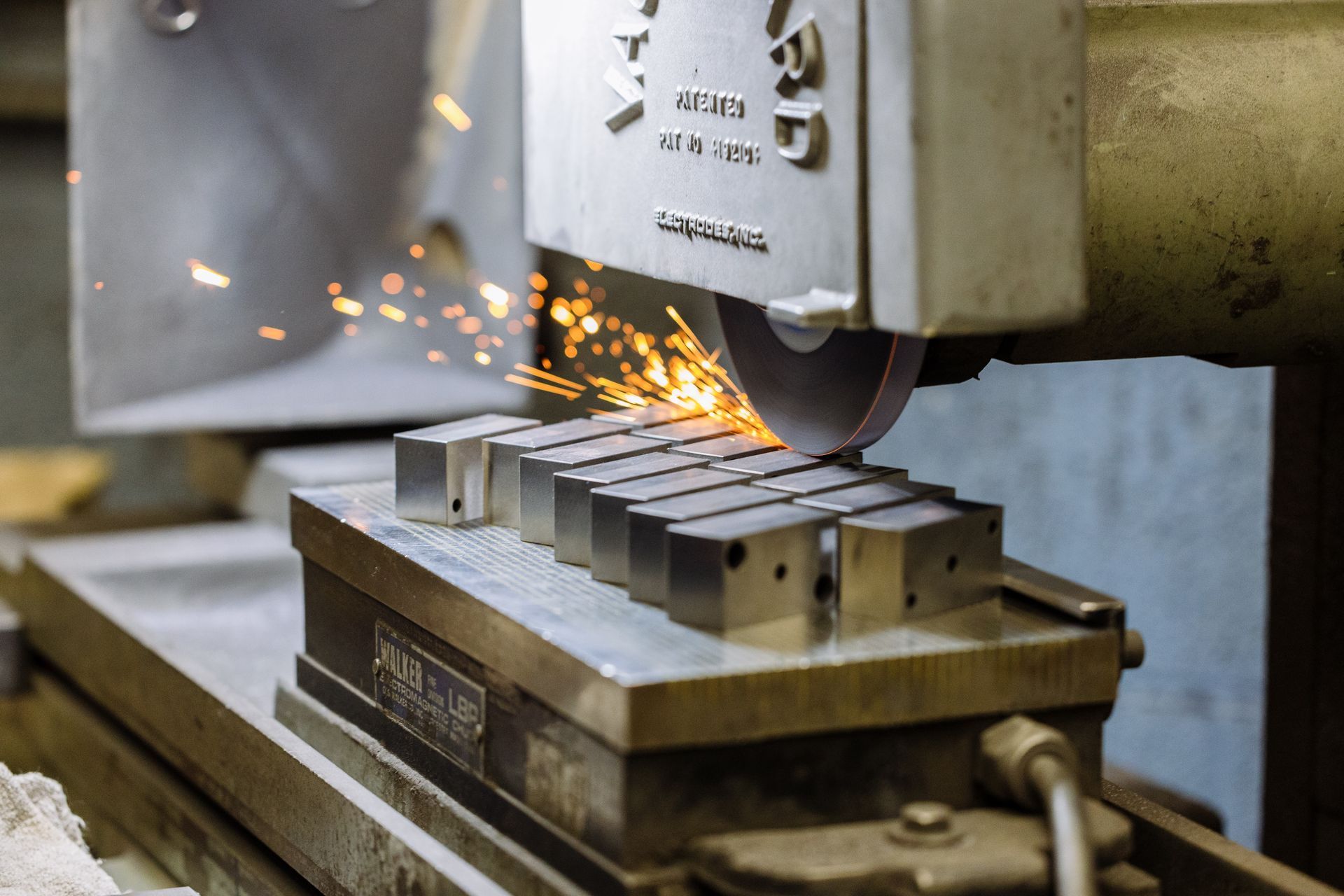