A Guide to How Wire EDM Works
Wire EDM, or Wire Electrical Discharge Machining, is one of the most precise and efficient manufacturing processes used today. At Modelcraft Co., we leverage this advanced technique to create intricate parts with tight tolerances, particularly for industries like aerospace, medical, and commercial manufacturing. In this blog, we’ll walk you through how Wire EDM works and why it’s such a powerful tool in precision machining.
What Is Wire EDM?
Wire EDM is a non-contact machining process that uses electrical discharges (sparks) to cut conductive materials. Unlike traditional cutting methods, Wire EDM doesn’t rely on physical tools to shape a part. Instead, it uses a thin wire, typically made of brass or copper, as an electrode to remove material with incredible accuracy.
This process is especially effective for creating complex shapes, fine details, and components with tight tolerances that would be difficult or impossible to achieve using conventional machining techniques.
How Does Wire EDM Work?
1. The Wire and the Workpiece
The process starts with a thin wire, often ranging from 0.004 to 0.012 inches in diameter. The workpiece must be made of a conductive material, such as steel, aluminum, or titanium. The wire and the workpiece never touch; instead, they are separated by a dielectric fluid, usually deionized water, which helps to control the electrical discharge and cool the cutting zone.
2. The Electrical Discharge
When a voltage is applied between the wire and the workpiece, an electrical spark jumps across the gap, removing tiny amounts of material. This discharge occurs thousands of times per second, precisely eroding the material along the programmed path.
3. Controlled Movement
The wire is controlled by CNC (computer numerical control) technology, which ensures precise and consistent movement. The machine can follow complex paths, enabling the creation of intricate designs, sharp corners, and tight radii. The wire is continuously fed from a spool to ensure a fresh, clean electrode is always in use.
4. The Role of the Dielectric Fluid
The dielectric fluid plays a critical role in the Wire EDM process. It cools the workpiece, flushes away debris, and prevents unwanted electrical arcing. This allows for smoother finishes and ensures high accuracy in the final product.
New Paragraph
Applications of Wire EDM
Wire EDM is widely used across industries where precision and complexity are essential:
- Medical Devices: Intricate components for surgical instruments and implants.
- Aerospace: Engine components, turbine blades, and structural parts.
- Tool and Die Making: Creating molds, punches, and dies with intricate details.
- Electronics: Manufacturing small, precise components for circuit boards and connectors.
Contact Modelcraft For Wire EDM
Wire EDM is a powerful machining method that combines precision, versatility, and efficiency. Its ability to handle complex geometries and hard materials makes it indispensable for industries that demand high-quality parts with tight tolerances. At Modelcraft Co., we use Wire EDM to solve our customers' toughest manufacturing challenges and deliver exceptional results.
If you’re looking for a trusted partner in precision manufacturing, contact us today at
(860) 453-9493. Let’s work together to bring your designs to life with unparalleled accuracy and quality.
Recent Articles
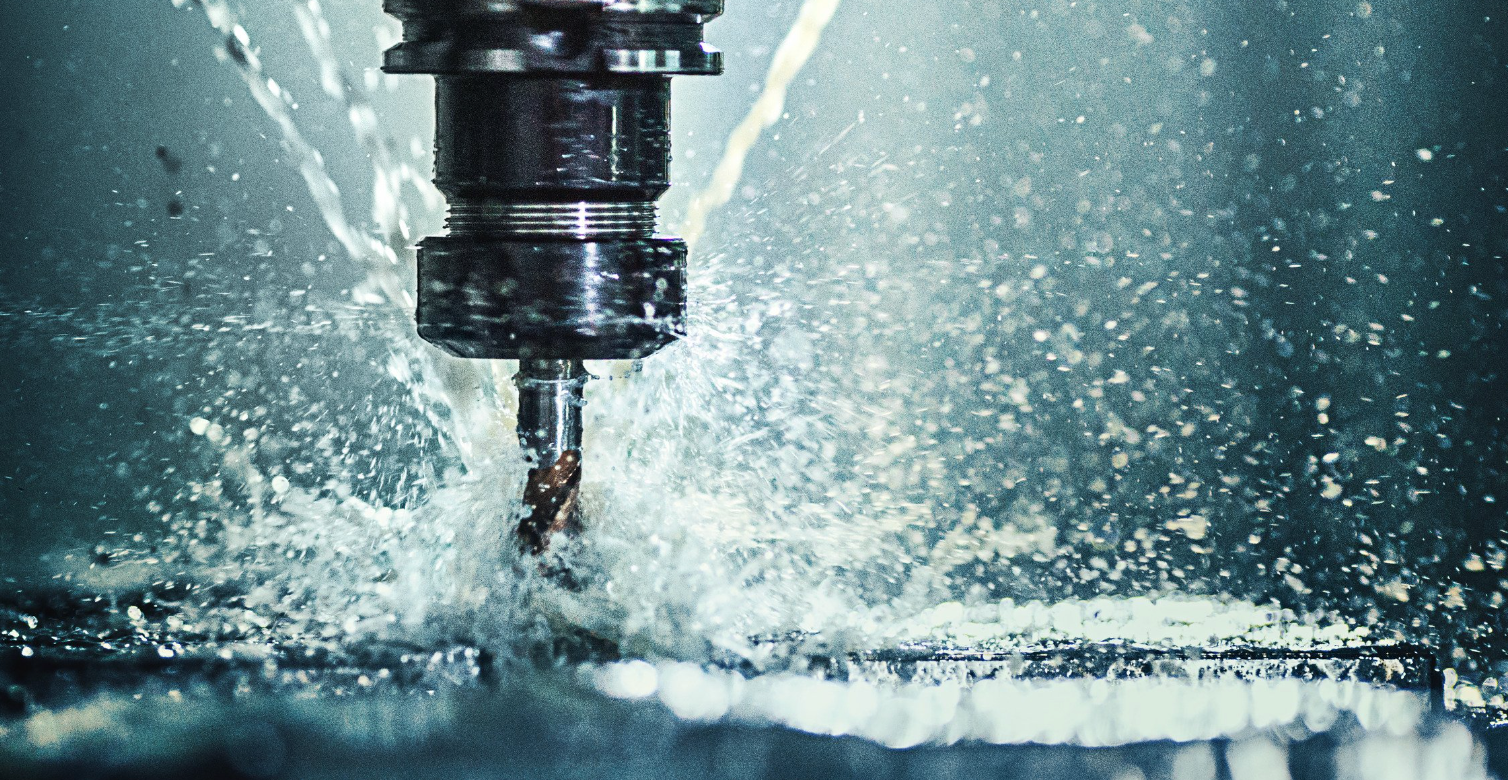
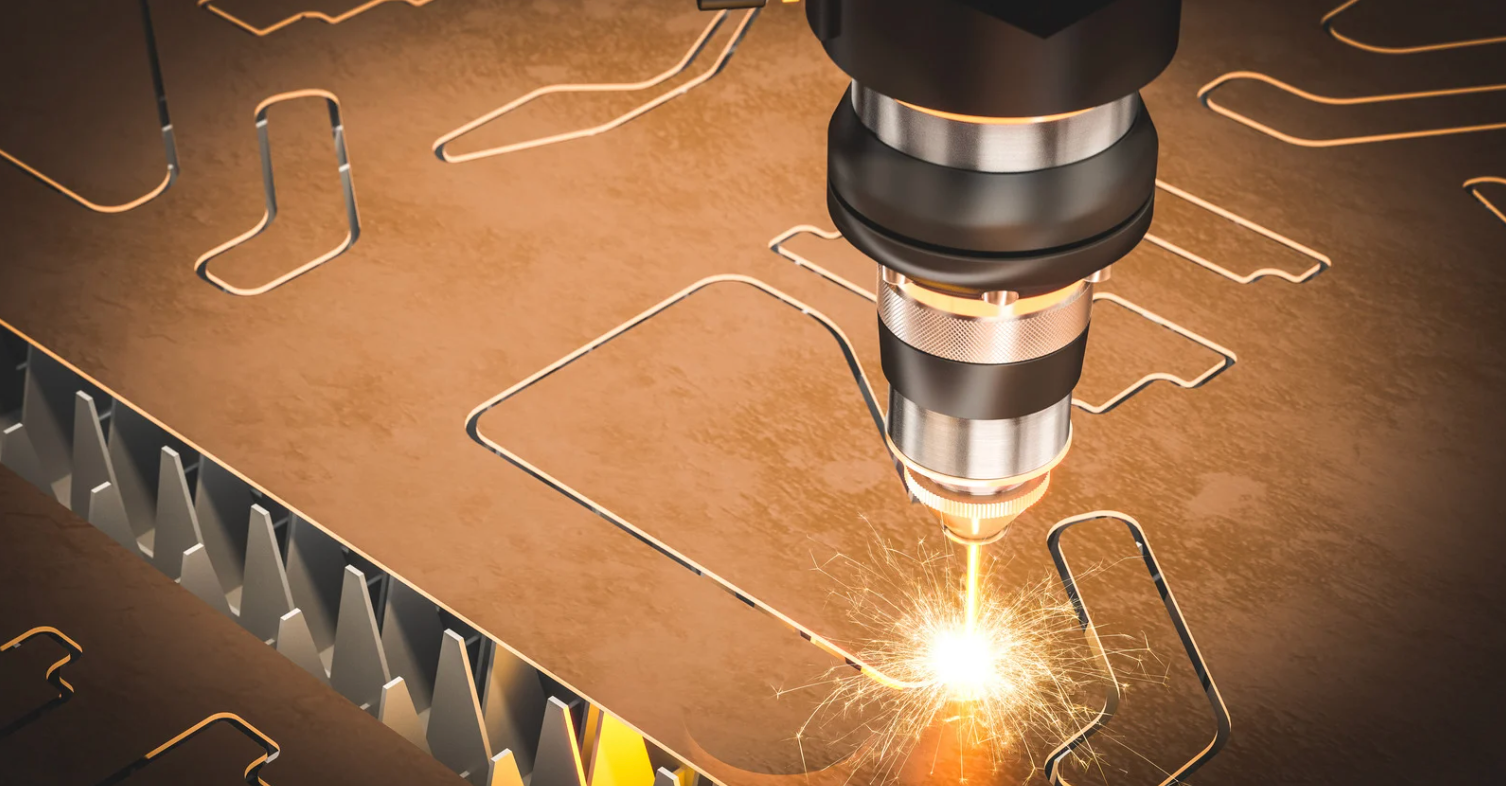

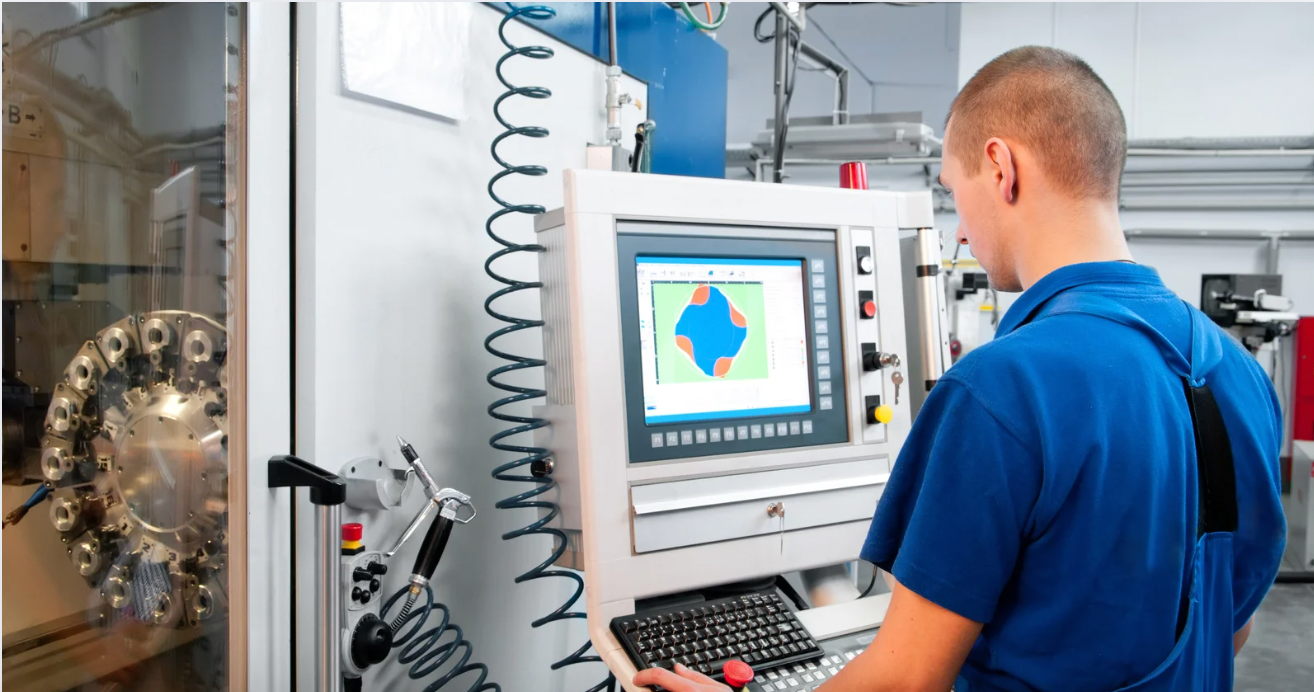
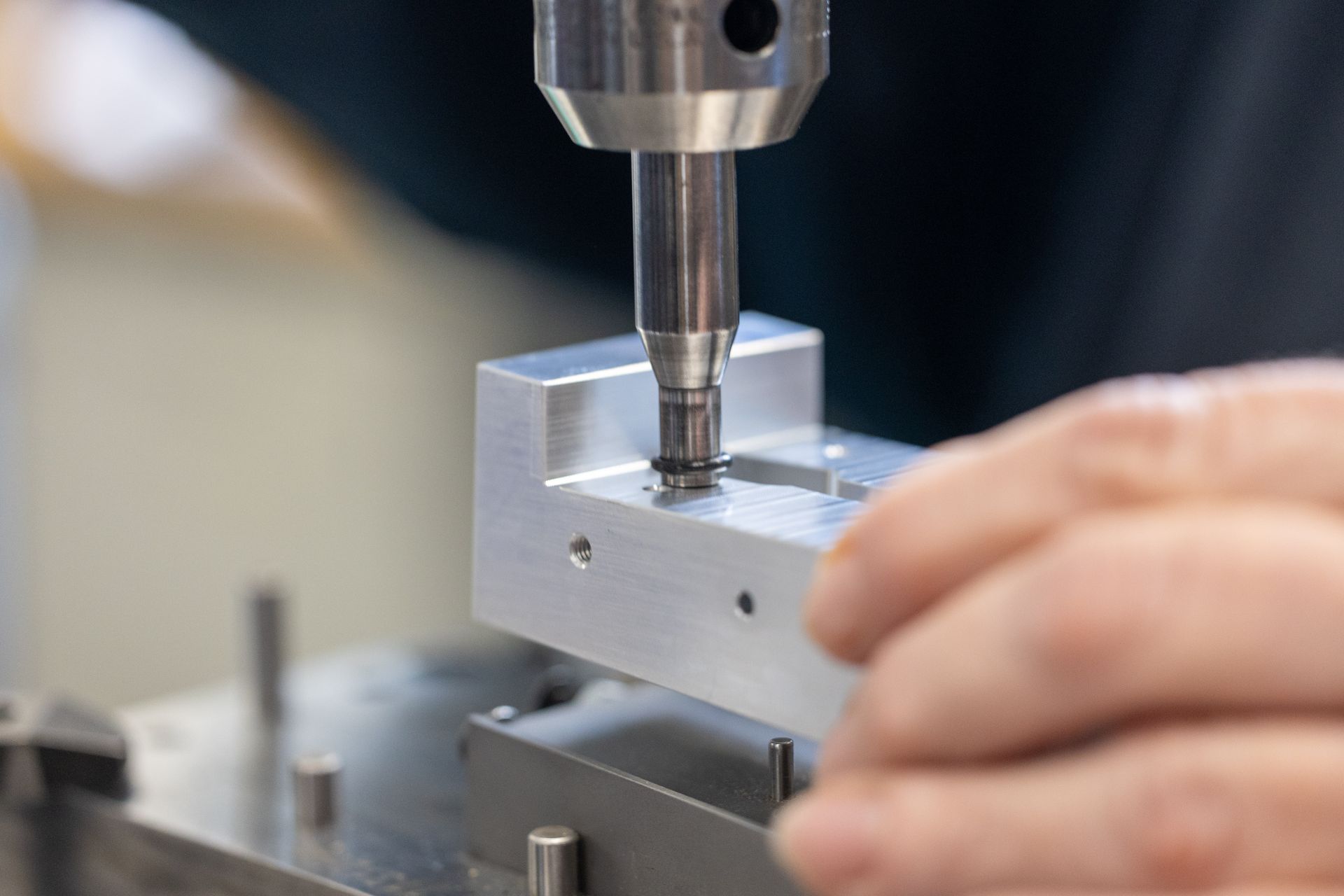
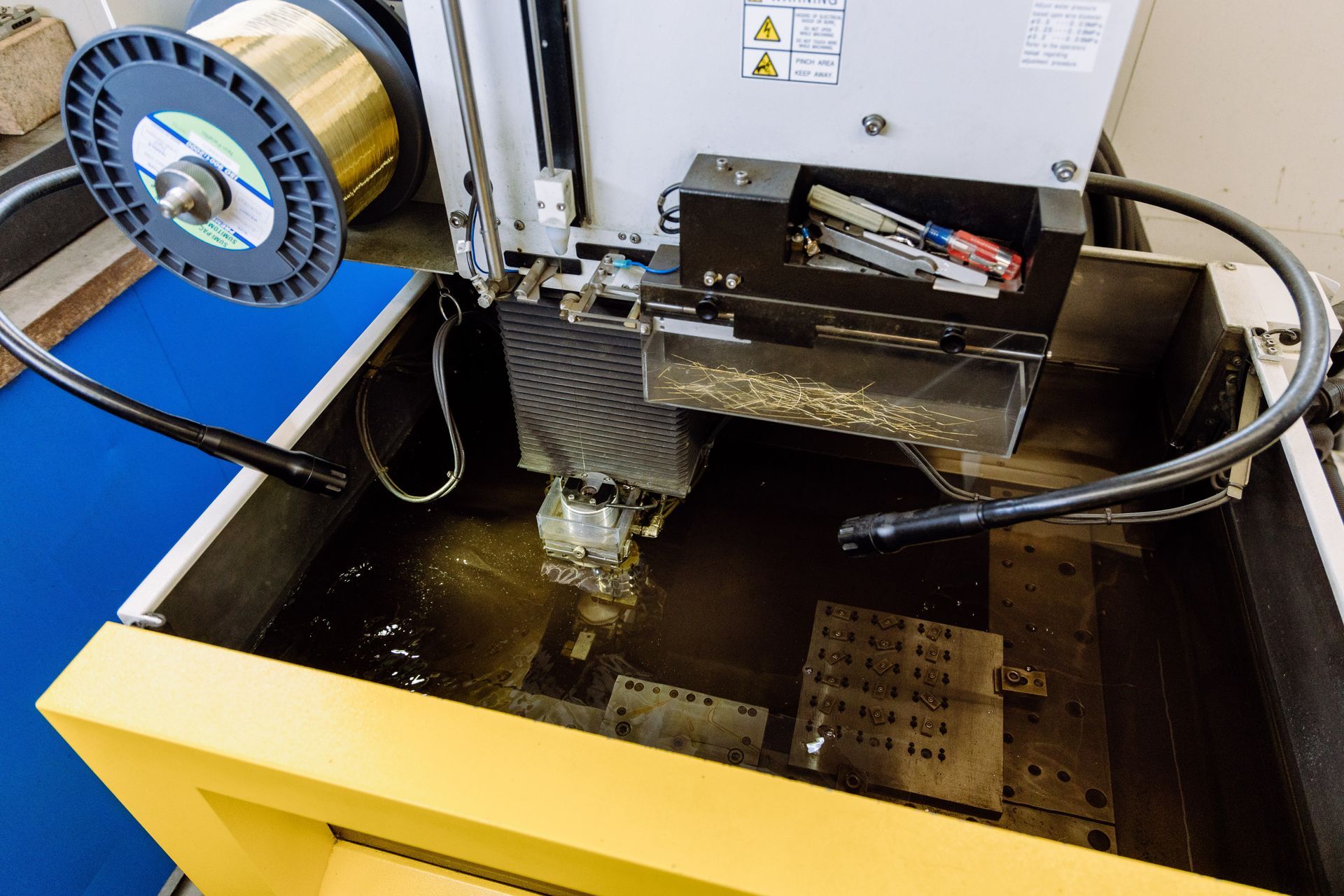
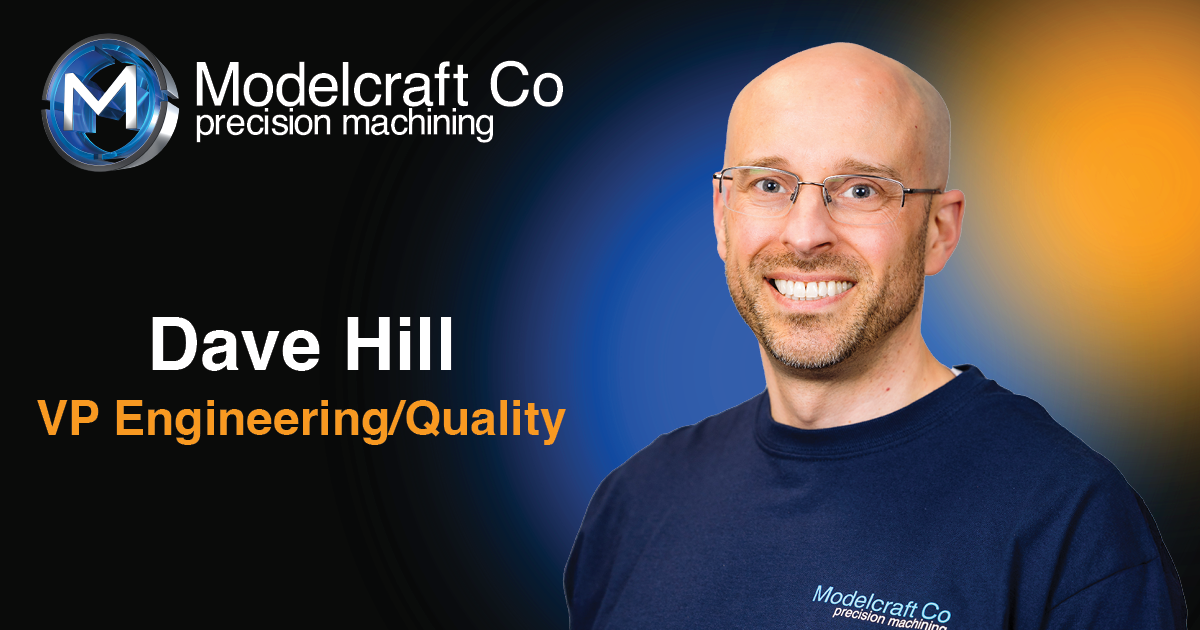
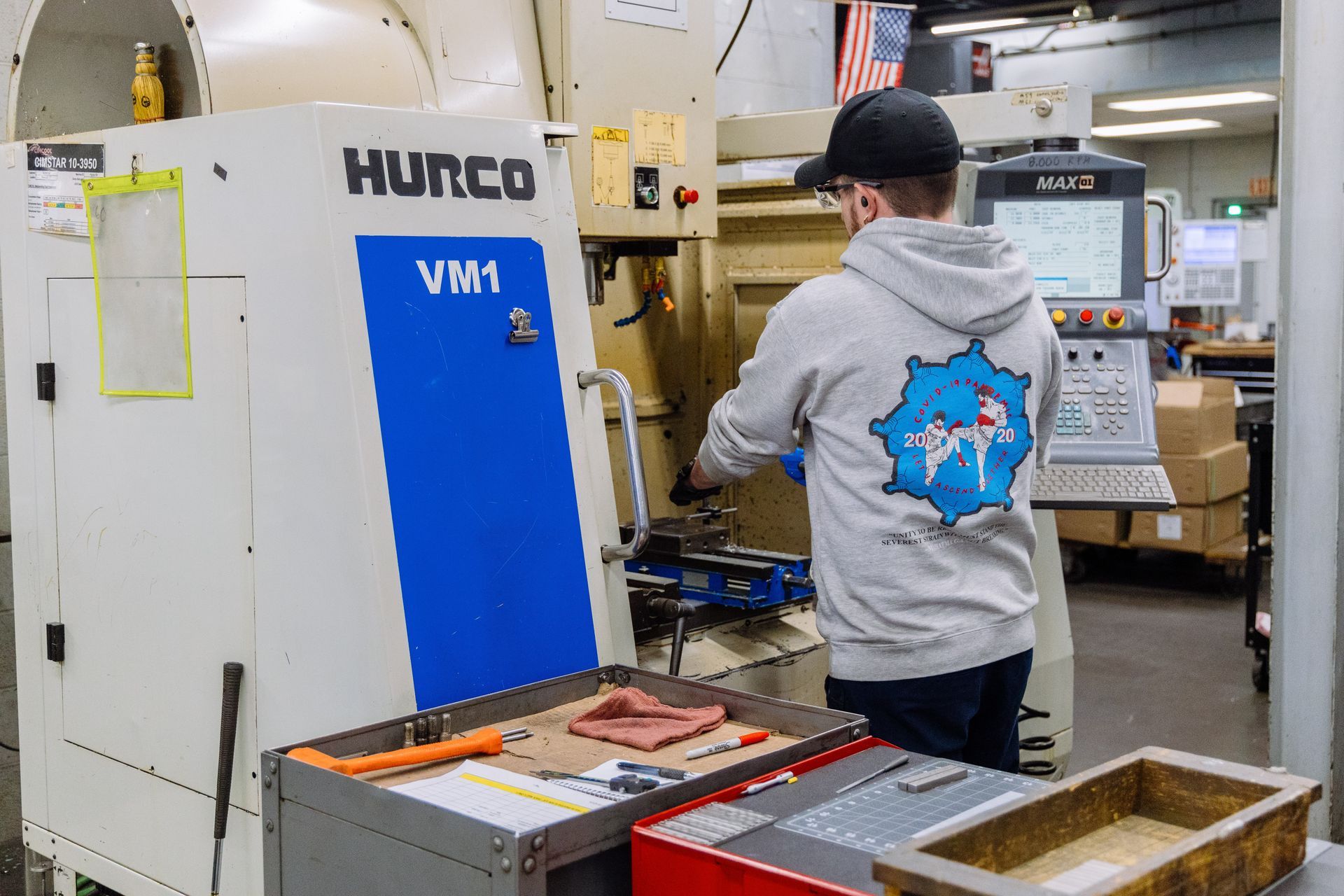
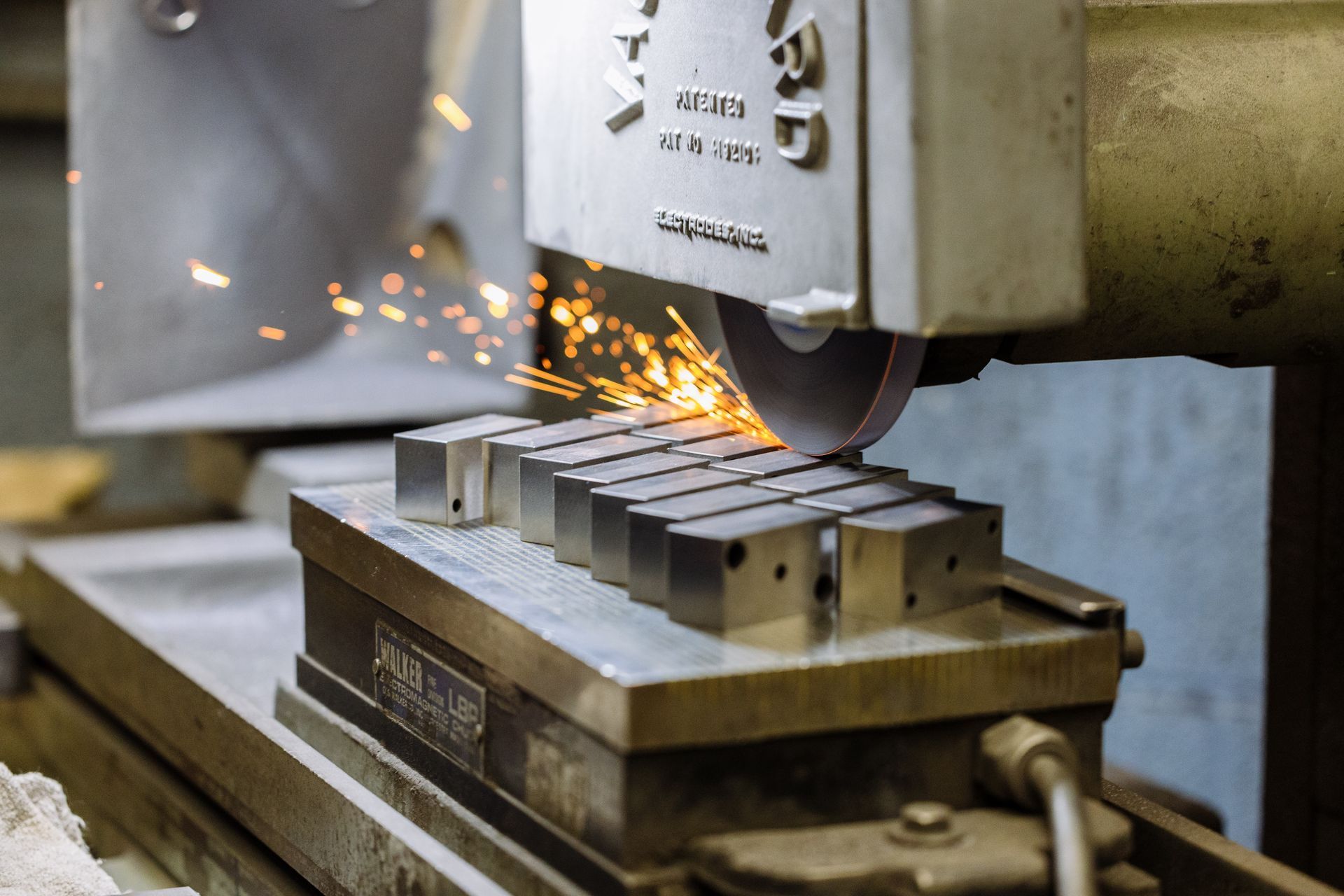